Manufacturing Epoxy Flooring
Epoxy coatings have had a strong and positive history in refinishing concrete floors for many years. Their high adhesive qualities and durability have made them the primary “go to” for refinishing. They are known for very good resistance to chemicals as harsh as sulfuric acid and other highly caustic substances.
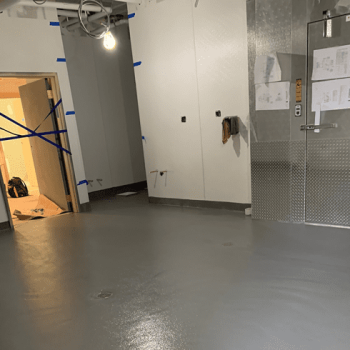
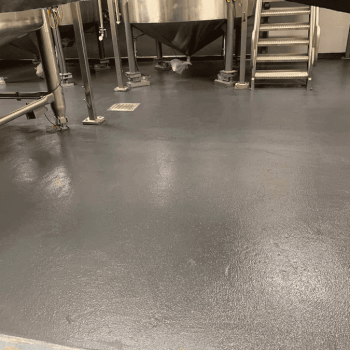
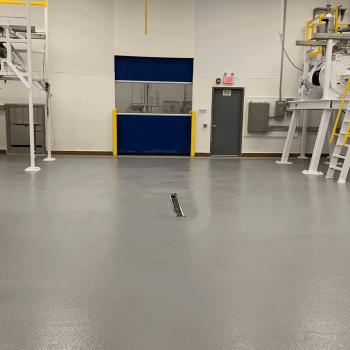
Epoxy coatings cause no issues with the alkali in concrete, unlike less durable polymers, they provide great durability as coating used in manufacturing facilities. Unlike paints, epoxies are three-dimensional and form thicker layers on top of concrete therefore last much longer and are resistant to wear.
Epoxy coatings guarantee seamless coverage and are the best choice for refinishing worn concrete floors versus any other coatings. They work especially well, even with newly modified patch materials such as polyureas and urethane cements. They are often used to fill cracks and dents spalling before the coating is applied. Their resistance to substantial thickness protects the base concrete floors well, from the effects of contaminants, chemicals and abrasion which would easily damage plain cement which often cracks, crumbles or delaminates.
How to Have Successful Coating
Manufacturers need to look at the total cost/benefit – while epoxy coating may seem pricey and does require some downtime while it is applied and cures, the benefits easily compensate for both the money and time spent during the process.
Consider the cost of lost productivity and time if you have an “obstacle course” of worn concrete.
Philadelphia Epoxy Flooring is always happy to help educate customers and provide a thorough inspection before recommending any application. If there are only relatively minor gouges, spalling, scrapes, or smaller cracks to be filled, judicious use of an epoxy filler designed for filling those kinds of damage can be quickly and easily done.
We provide technical advice on handling significantly damaged areas, which can be repaired before coating using various patching systems prior to the installation of epoxy/resinous coating. This should be timed so that the entire area has had time to cure BEFORE the coating is applied to avoid degradation of the final finish.
Concrete emits vapor, so transmission rates should be checked prior to any new coating process. A concrete vapor control epoxy primer may be required if inspection/testing shows that vapor transmission rates exceed manufacturer specifications.
When vapor transmission rates are exceed manufacture specifications, a concrete vapor epoxy primer can be used to rectify the issue.
Having a clean concrete surface is critical. After any oils or other contaminants have been removed, the surface needs to be ground down to provide a solid bond between it and the epoxy coating to be applied. This sets the stage for the coating to be applied.
For the best results, a proper application normally requires a three-day process that may be accomplished in stages to avid help avoid production and lost down time enabling a facility to continue production throughout the process. Following a 3-coat, 3-day process, ensure high quality and longevity.